製造業DXとは? ~注目される理由から課題や事例まで解説~
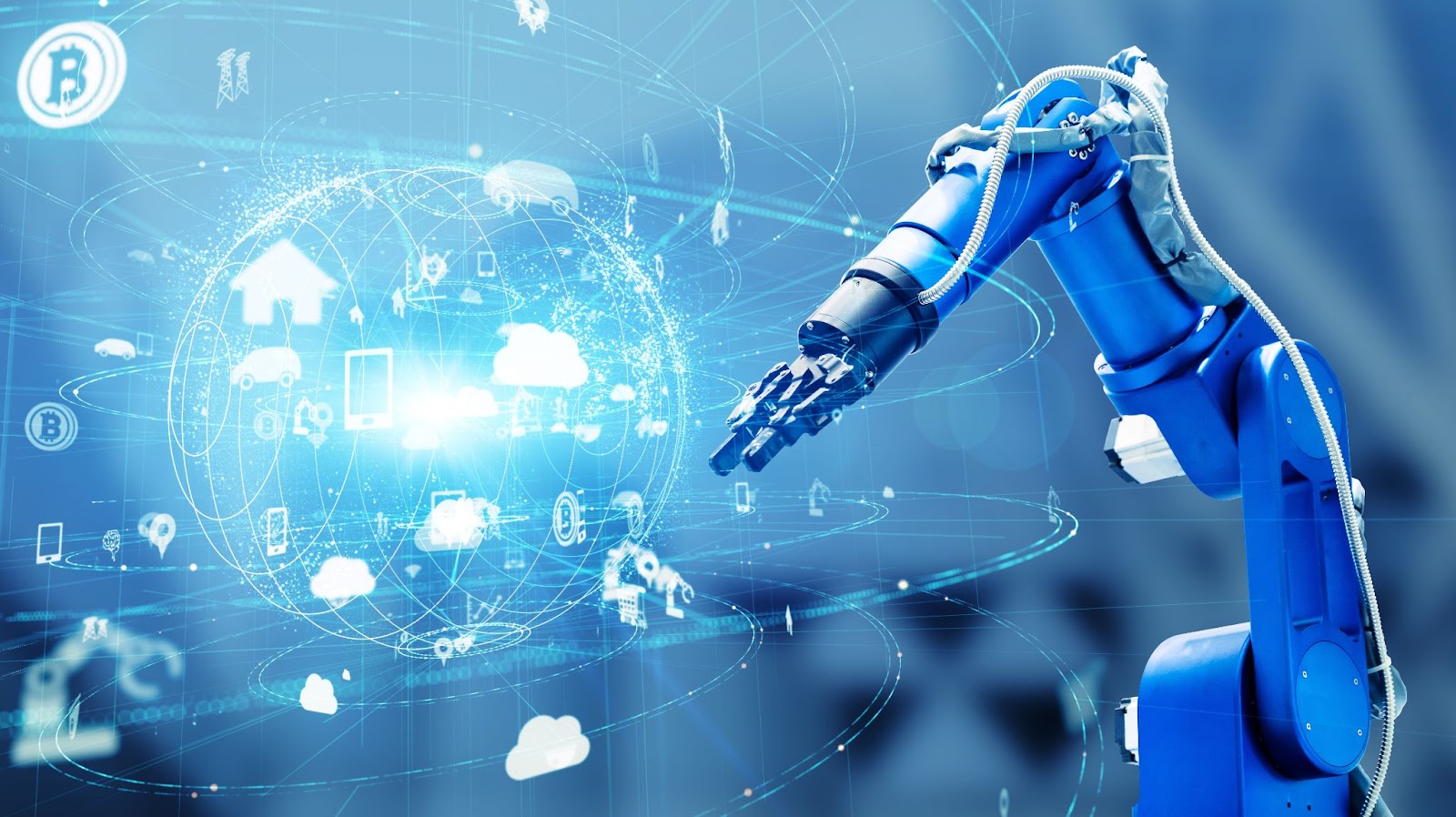
製造業DXとは、製造業におけるDXのことで、最新のデジタルテクノロジーを活用することで、製造業が生み出すプロダクトや業務プロセス、ビジネスモデルなどを変革させることを指します。
経済産業省の主導などにより、業界や部門を問わず、日本全体でDX(デジタルトランスフォーメーション)の機運が高まっています。
2025年の崖を回避するために、また、デジタルディスラプションが起きている市場において競争力を維持・向上するために、そして、人々の暮らしをより便利に豊かにするために、DXは必要です。
今回は、製造業界に焦点を当てて、DXを推進する際の課題や具体的な事例をご紹介いたします。
【関連記事】
DXの成功事例から成功させるポイントまでをご紹介
DX人材に求められる役割とマインドセットを簡単解説
DX時代に求められるセキュリティ対策とは
働き方改革とDXの関係性とは?~DXを活用して働き方改革を実現する方法~
DXリテラシーとは? ~ITリテラシーの違いから現代においてDXリテラシーが求める背景を一挙ご紹介~
金融業DXとは? ~金融業DXにおける課題と成功事例を解説~
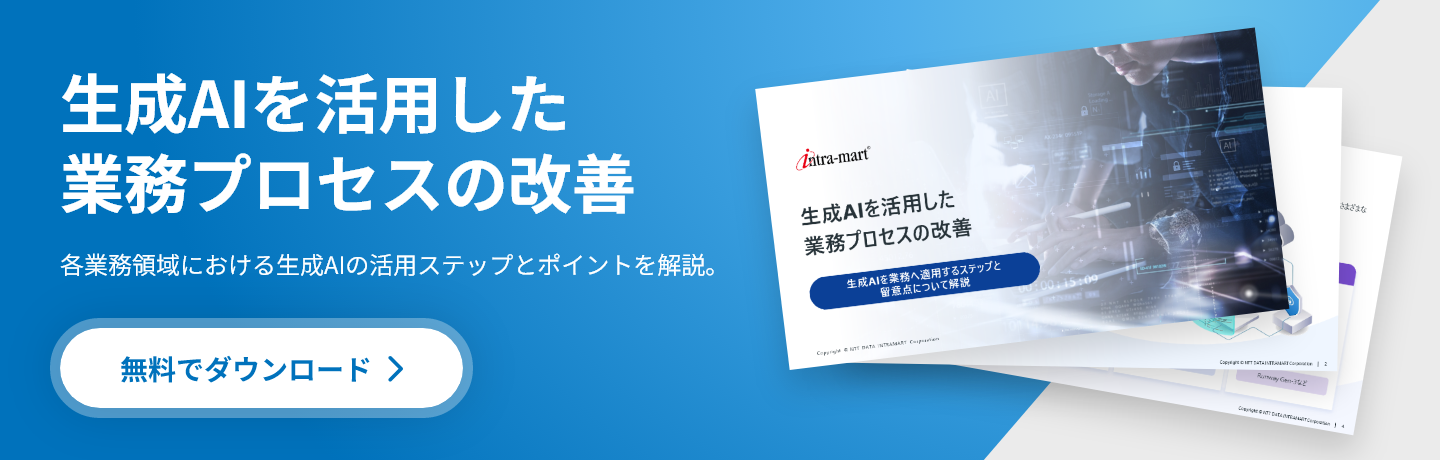
1. 製造業DXとは
製造業DXとは、製造業におけるDXのことです。最新のデジタルテクノロジーを活用することで、製造業が生み出すプロダクトや業務プロセス、ビジネスモデルなどを変革させることを指します。
業務が属人化しやすい製造業において、DXの高い効果が期待されています。
製造業でDXが注目されている理由について詳しくは、次章でお伝えいたします。
製造業でDXが注目されている理由
製造業においてDXが注目される理由や期待されている効果は、主に次の4点です。
商品に付加価値をつけられる
「ものづくり大国」として世界に知られる日本は、欧米に次いで製造業の歴史が長い国です。戦後、製造業大国ドイツとともに高い輸出シェアを誇ってきましたが、90年代以降、シェアは低下しました。
一方のドイツはシェアを維持しています。勝因は、付加価値の高い製品づくりに注力することで日本のように中国や韓国との価格競争に巻き込まれなかったためであるとの指摘があります。
国内に目を向けても、かつてのようにモノが売れた時代ではなくなりました。モノがあふれて市場は飽和状態にあり、消費者の志向はモノからコト(体験)へとシフトしてきています。
国際的な競争力を強化するためだけでなく、国内市場で生き残るためにも、DXに取り組んで製品に付加価値をつけたり、製品のサービス化を行ったりして、商材を変革させる必要があるのです。
製造現場を半自動化できる
DXは、製造プロセスの変革にも有効です。
これまで人手で作業やチェックを行っていた部分を、AIやRPAといったデジタルテクノロジーに任せることで、スピードの向上やミスの低減、質の向上などが期待できます。
また、それまでは部分的に独立してデジタル化していたものを、全体でつないだ上でデータを取得・分析することで、新たな示唆が得られる可能性があります。
既存の製造ラインを半自動化することができれば、業務効率化だけではなく、人件費の削減にもつながります。
製造設備のメンテナンスコストを削減できる
製造設備にIoTなどを導入することで、既存のメンテナンス方式でかかっていたコストを削減できる可能性もあります。通常、製造設備のメンテナンスには「定期メンテナンス」「予防メンテナンス」「事後メンテナンス」の3つの方法があります。
ただ、いずれの方法にも欠点があり、定期メンテナンスや予防メンテナンスは、メンテナンス作業そのものが無駄になる可能性が、事後メンテナンスでは製造設備がストップしている間に製造が行えなくなるロスが発生します。
一方、製造設備にセンサーを取り付けるなどすれば、機械の作動状況や、不良品の発生率の変化などから故障しそうな部品を察知して、タイミングよくメンテナンスを行うことができ、無駄を最小限に抑えられます。
属人化していた業務を平準化、継承できる
製造業や建設業では、少子高齢化による人手不足や従業員の高齢化が特に深刻化しています。また、ものづくり産業では、熟練の職人に蓄積された暗黙知の若手への継承や、ベテランでないと行えない業務の属人化が課題となっています。
こうした製造業特有の課題解消にもDXが有効です。
たとえば、AR/VRゴーグルやスマートグラスを新人技術者に装着して指導に活用したり、ワークフローツールを導入して業務を平準化したり、熟練の職人の作業からデータを蓄積してロボットのプログラムに活かすなどです。
高齢化が進み、退職時期が近づいている熟練技術者の技術を消失させず、社内にナレッジとして蓄積できるようになります。
2. 製造業DXにおける課題
ただ、製造業においてDXを推進する上では課題もあります。
主に「DXに必要な人材が不在」「自社に最適なデジタル技術を選定するハードルが高い」といったことが挙げられます。
DXに必要な人材が不在
製造業に限らず、DX推進担当者には、自社の属する業界や自社のビジネスに加え、基本的なIT、幅広いデジタル技術に関する知識が求められます。
ただ、すべての製造業企業にそうした人材がいるわけではなく、「DX人材がいないためにDXを進められない」という問題が生じます。
経済産業省が発表した「デジタルトランスフォーメーションを推進するためのガイドライン(DX 推進ガイドライン)Ver. 1.0」では、DX推進は経営者の意思決定から始まり、DX推進チームを編成するという流れを推奨しています。この時、必要なDX人材の確保については、社外からの獲得や連携も視野に入れることが補足されています。社内の人材で対応しきれない場合は、新たに必要なスキルを持った人材を採用したり、デジタルツールのベンダーに協力を仰ぐといった解決策が考えられます。
【関連記事】
DX人材に求められる役割とマインドセットを簡単解説
自社に最適なデジタル技術を選定するハードルが高い
製造業で活用できるデジタル技術には、IoTやウェアラブルデバイスなどがありますが、同じ製造業といえど、それぞれ製造物や製造工程、経営戦略などが異なるため、「このデジタル技術を導入すればDXに成功する」といった画一的な成功パターンはありません。
また、デジタル技術も日進月歩であるため、新たな技術やサービスにキャッチアップして、自社のビジネスに役立つかどうかを検討していく必要があります。
このため、自社に最適なデジタル技術を選定して導入し、さらに活用していくことは、簡単なことではありません。経営層やDX推進チームを中心に選定を進め、現場の声も聞きながら導入する技術やツール、ベンダーなどを決定する必要があるでしょう。
3. 製造業界におけるDX事例
他社の取り組みをそのまま真似ることはできなくても、抱えている課題や製造物が近しい場合は、事例は参考になるはずです。
ここでは、製造業界で先進的な取り組みを行っているDX事例を、経済産業省が発表している「製造業DX取組事例集」から5つピックアップしてご紹介いたします。
「工場IoT」で問題発生を未然に検知(トヨタ自動車株式会社)
日本最大手で、世界最大の自動車メーカーの1つであるトヨタ自動車では、それまで、3D CADデータや試作時の特性データといった個々のデータ活用においては成果を上げてきたものの、次のような課題を抱えていました。
課題
同社では、すでに3D CADデータや試作時の特性データ、お客様から得たデータなどを技術開発・生産準備に役立てて一定の成果は上げていたものの、個々のデータ活用の範囲を超えるものではありませんでした。
また、これらの情報を技術開発へタイムリーにフィードバックできていなかったといいます。
さらに、ドイツ政府が推進しているIndustry4.0や、非自動車メーカーのEV市場への進出など、ビジネスを取り巻く国内外の環境の変化に危機意識を持っていました。
取り組み
そこで同社は、全社的なデジタル化を検討し、手始めに「工場IoT」に着手しました。「工場IoT」では、2~3年かけて工場横断の共有プラットフォームを構築。その上で、たとえば、エンジン部品加工設備においては、稼働率低価やばらつきの要因として工具交換を特定し、工具設定や加工精度、設備切削負荷などの情報の変化点と相関を把握しました。それらの情報から、さらに原因を推定して、対策ポイントを特定したといいます。
ハード面のデジタル化と同時に、ソフト面の対応として、社員に対する組織的な教育支援を行い、プラットフォーム上にはBI・AIなどの便利なツールを整備しました。
成果
前述のエンジン部品加工設備においては、ビッグデータから特定した要因をもとに実機に対策することで、問題の発生を未然に検知することに成功しました。
データを収集・蓄積する際も、トヨタ生産方式の考え方に則り「必要なものを、必要な時に、必要な分だけ」に限定するなど、ムダなデジタル化を行わなかったことも功を奏し、全体として費用対効果が上がったといいます。
この成功を受けて、エンジニアリングチェーンやサプライチェーンを含むデジタル化への適用を打ち出し、品質向上や商品力向上、法規への対応など、付加価値向上に関わるデジタル化に着手しました。
「マス・カスタマイゼーション」を実現するため、デジタル・ファクトリーを設立(ダイキン工業株式会社)
空調機、化学製品メーカーのダイキン工業は、世界五大陸38ヵ国に拠点を持つグローバル企業です。同社では、従来、多品種混合生産や需要変動に柔軟に対応できるよう、生産ラインの工夫に取り組んでいました。
課題
市場環境変化のスピードが上がってきたことなどから、製造コストの削減と製品差別化による競争力強化を図る必要性を感じ、「マス・カスタマイゼーション」を掲げたモノづくりをスタートしました。
取り組み
「マス・カスタマイゼーション」として、
- サプライチェ―ンの最適化(生産の効率化、ニーズに対応した生産計画・在庫管理)
- エンジニアリングチェーンの最適化(要求分析・システム設計・コンポーネント設計)
- 情報領域の深化(データ連携やモデリング・分析とサプライチェーンやエンジニアリングチェーンへのフィードバック)
これらの実現に向けて、エンジニアリングチェーンとサプライチェーンにおけるすべての情報をネットワークでつないだ「デジタル・ファクトリー」を構築しました。
実際に、大阪・堺に新工場(デジタル・ファクトリー)を設立。
工場内のIoT活用サイクルとして、「製造現場データの発掘、データの収集と統合、データの見える化と分析、顧客への価値提供」を回す構想が作られました。
生産データをリアルタイムで可視化・分析し、スピーディに生産現場の課題解決を行うために、工場内に「工場IoTプロジェクトセンター」を設置。ここにメンバーが集まり、データに基づいた議論や判断を行っているといいます。
さらに、各海外拠点とも「工場IoTプラットフォーム」を連携して、グローバルでの利活用を行っています。
成果
「デジタル・ファクトリー」の設立により、生産状態を可視化することで、生産計画の最適化を実現。ロスを低減させられたといいます。
また、予測技術の確立や人の判断基準のモデル化、人やモノの動きのデジタル化、工場のデジタルツイン構築(生産シミュレーション)などを通して、さまざまな予知・予測を実現しました。
自社の成功を元に現場データ活用サービス「i-BELT」をサービス化(オムロン株式会社)
大手電気機器メーカーであるオムロンでは、自社を含む日本企業全体に対してデジタル化における課題感を抱えていました。たとえば、日本企業のデジタル化を阻む要因として、日本企業のヒエラルキー的な特徴による現場と各部署との断絶や、分業化による総合的な知識・技術を兼ね備えた人材の不足、社内外とのコミュニケーション・情報連携不足、対グローバルでの競争力の低下などを挙げています。
課題
同社では、日本で開発・設計した後、工程設計以降をグローバルで行うことがあるため、データ活用に優先して、運用の確立や、ものづくり・設計思想のカルチャーの融合について考える必要があり、その後、標準化に向けたデータの流れを考える必要があったといいます。
取り組み
オムロンの20万種に及ぶ制御機器群と60年以上にわたり培った現場経験を活かした、オムロン独自の現場データ活用サービス「i-BELT」を開発し、「生産管理」「品質管理」「設備効率」「エネルギー」 の4つの切り口で、自社に向けて展開。
成果
「i-BELT」の活用により、製造現場における作業効率の安定化や工具の摩耗量の削減、加工時間の削減などを実現しました。
さらに、自社の成功を糧に、当初の課題感から、日本のデジタル化促進へと繋げるべく、「i-BELT」をサービスとして社外へ展開。暗黙知の形式化と現場モチベーションの向上を通して、日本企業のデジタル化の推進に貢献しています。
事業の可視化と整理が、業務改善や経営戦略につながった(株式会社今野製作所)
油圧ジャッキや油圧爪付ジャッキなどの製造販売を手がける今野製作所では、事業のスタイルをオーダーメイド型に移行することで、高付加価値化へのシフトを検討していました。
課題
上記のように、事業のシフトを検討していた同社ですが、社内では各組織で個別受注への対応力不足、負荷集中、納期遅れなどが起き、体制が整っていませんでした。
また、事業規模が小さいにも関わらず、受注生産、見込生産など多様な生産形態が混在していることが判明し、業務の整流化が必要でした。
取り組み
まず、業務プロセスの分析ツールを活用することで業務を可視化し、自社に合った生産プロセスを整理しました。
また、業務プロセスを最適化するために、必要なITツールを小規模で社内開発し、これを業務の改善に活用しました。
こうした取り組みに当たり、企業規模が小さいこともあり、社内にDXに関する知見がなかったため、外部の専門家の援助を受けながら、自社内の人材の適性を見極めつつ推進することで、主体的に改革を行う風土を醸成していったといいます。
専門家だけでなく、中小企業同士でサークルを作ってシステムツールの開発に関する情報交換を行うなど、外部と積極的に交流し、知見を増やしていったこともポイントです。
成果
自社の生産形態を含めた整理を行うことで、部署間に人手でデータ入力を行うプロセスが存在することが明らかになり、データを自動流用できるような業務改善につながったほか、生産形態の特性に合わせて既存事業の位置づけを変えるという戦略の変革にもつながりました。また、事業の高付加価値化に向けて、従来着手できていなかったビジネスを取り込むこともできるようになりました。
(オークマ株式会社)
大手工作機械メーカーであるオークマでは、主力製品としてNC工作機械を製造販売していました。このNC工作機械の開発や、当時の標準化への機運の高まりがDXのきっかけとなりました。
課題
上記のように、NC工作機械の開発、そして、当時の標準化への論調を通して、社内的に「個別最適」ではなく「全体最適」を指向しようという機運が高まったといいます。
そして、そのためには、経営学者の野中幾次郎氏が唱える「SECIモデル」を踏襲した「知識創造※」を促進することが重要だという考えに至ったのだそう。
※知識創造…従業員の頭の中に隠れている知識を掘り起こし、それを既存のデータや知見と組み合わせて問題解決のために有用な知識に昇華して、デジタル化された環境に取り込むこと。
取り組み
従来から行われていた自社のNC工作機械の設計から生産まであり方を改革するという意識を持ち、
- 設計から製造までデータをワンストップさせて行うコンカレント・エンジニアリング
- 変動する生産計画への柔軟な対応のための生産効率の最大化
- 人の入力や操作の蓄積と再利用のためのナレッジマネジメントを1つの生産システムに統合した生産モデル
成果
ナレッジマネジメントについては、情報をどのように知の創出につなげるかを検討する中で、従来、製造現場で行われてきたフランクナコミュニケーションや、知的生産の歴史について分析したといいます。これが奏功し、日本の製造業に合ったものを確立できたことから、「IT Plaza」として、製造業への「ものづくりサービス」として提供を開始しました。
NC加工機については、「自ら考え、成長するインテリジェントNC」(THINC)というコンセプトで、さらに発展させ、顧客や周辺機器メーカーなどをパートナーとし、共同でシステムやアプリケーションの開発を実現。こうして、トータルソリューションを創造する場を提供しました。
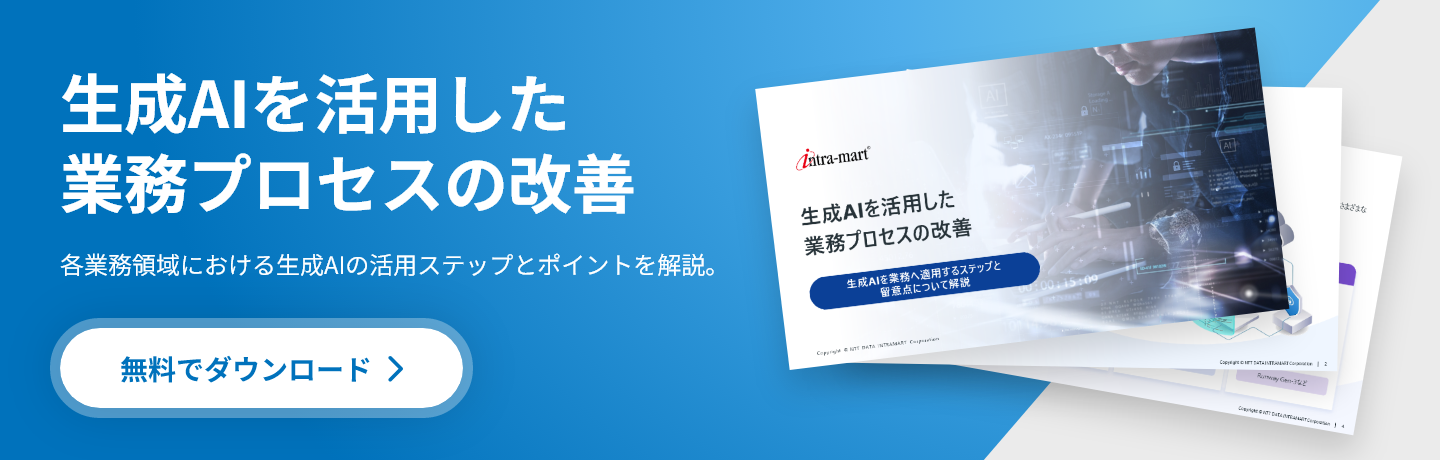
4. まとめ
製造業においても、他業界と変わらず、DXは必要不可欠なものといえます。特に、製造業における属人化や、少子高齢化に伴う人材不足、高齢化などの課題を解消し、モノが売れない時代に製品を「コト化」するためにDXは有用でしょう。
ここでご紹介した以外にも、DXの取り組み事例は続々と出てきています。自社の課題や状況を分析した上で、他社の例を参考にしながら最新のデジタルテクノロジーを上手に活用してDXを成功させましょう。
Concept Book
ローコード開発・業務プロセスのデジタル化で豊富な実績を持つintra-martが、お客様のビジネスにどのような効果をもたらすのか、特長や導入効果など製品コンセプトを詳しくご紹介しています。
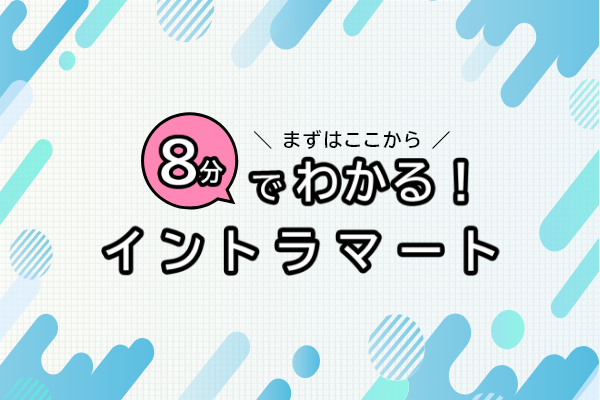
お困りごとがありましたら、お気軽にご相談頂ければと思います。